Самодельные станки | Мастер-класс своими руками
Бормашинка и ручная дрель
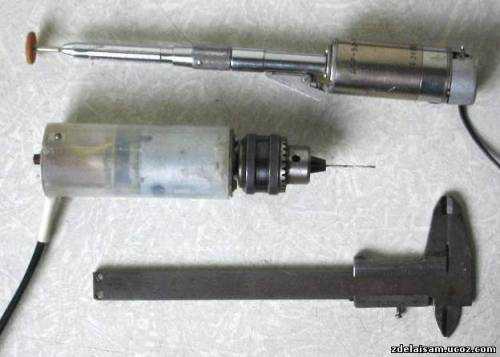
Бормашинка — двигатель ДПР-52, встречается в принтерах и фенах. Ручная дрель — двигатель от автомобильного компрессора, встречается в небольших тепловых пушках и фенах.
Бормашина 2
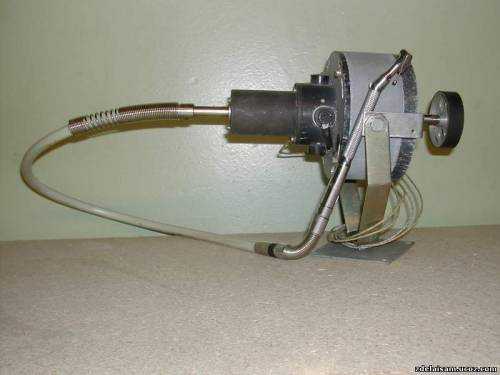
Бормашина со сменными наконечниками. Мотор PIV MTM, из лентопротяги вертикального магнитофона, болгарский. Таходатчик удален, на его месте закреплен гибкий вал бормашины. Вращение от оси мотора перадается на вал с помощью туго надетой пружины. Справа на оси укреплен алмазный диск для правки боров.Весь механизм закреплен в держателе с двумя степенями свободы и легко вращается влево-вправо, вперед-назад. Вся конструкция подвешена на рабочем столе справа вверху, не мешает работе. Можно утопить мотор в стол так, чтобы шланг бормашины выходил вертикально вверх.
Бормашина для гравировки
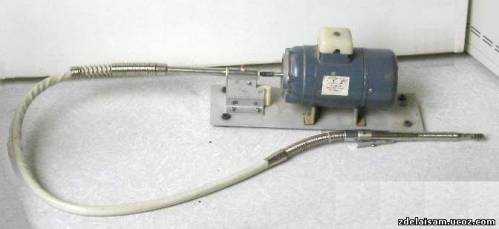
Бормашина для граверных работ. Мотор на 8000 об., шланг терпит до 10000. Мотор и шланг соединены пружиной, надетой на оси.
Дрель 1

Рукоять с механизмом от пневмодрели. Мотор передает вращение на турбину, насажен через переходное кольцо. В корпусе дрели уже находится планетарный редуктор примерно 3:1. Очень мощная машинка. Потребовались токарные работы: переходное кольцо, втулка на валу, подгонка конуса Морзе под размер 2а. Трудно было установить сильнотоковую кнопку.
Дрель 2
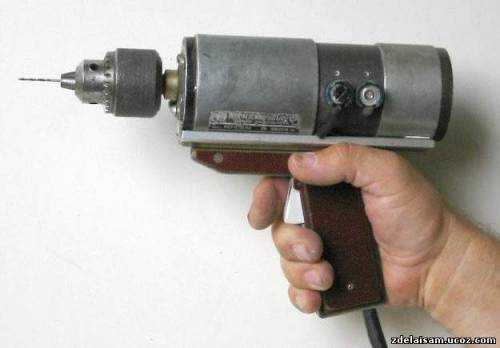
Мотор PIV 6 25/3A болгарского прозводства, работает от 5 до 40 В, от вертикального магнитофона/накопителя. Таходатчик (сзади) не используется, но хорошо уравновешивает всю конструкцию. Кнопка воздействует на контактную группу от утюга, мощная и не обгорает.
Отрезной станок 1
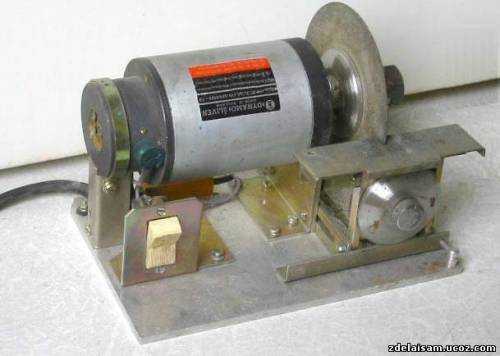
Отрезной станок 1 сделан под неармированные абразивные диски толщиной 0,5-2 мм. Перемещаемый столик. Виден «тормозной» резистор.
Отрезной станок 2
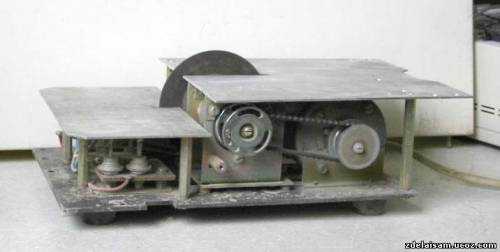
Отрезной станок 2 сделан под неармированные абразивные диски толщиной 0,5-2 мм. Два рабочих положения, с верхнего и нижнего столиков, так что мотор с реверсом. Отрезаю платы, делаю ключи, вырезаю каркасы для трансформаторов.
Сверлильный станок 1
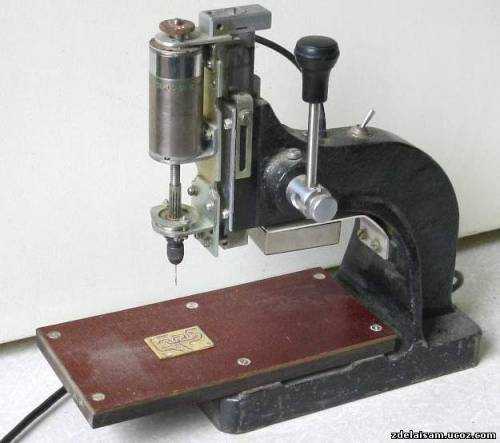
Сверлильный станочек с цанговым патроном на 0,8 мм. Сделан из остатков механизма, который назывался «пресс для изготовления аллюминиевых бирок». Двигатель ДПР-52, ось я удлинил только для красоты всей конструкции. Ход сверла — 20 мм. Видна коробка для сверл и абразивный диск на оси движка вверху для правки сверл.
Свелильный станок 2
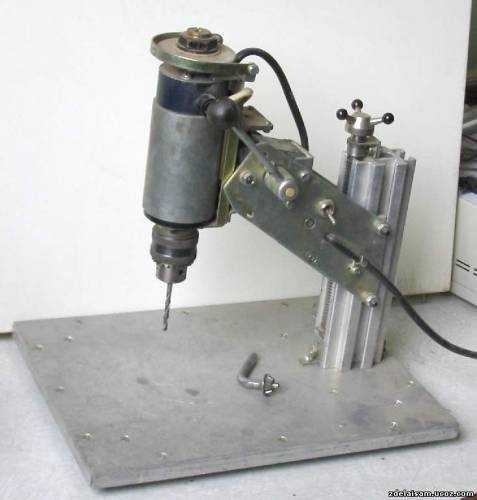
Свелильный станок под патрон 2а. Стойка из аллюминиевого профиля в нем червячная передача, с ее помощью каретка на подшипниках перемещается на 80 мм под сверла разной длины. Ручкой перещается собственно мотор еще на 20 мм. Вверху на оси мотора — абразивный диск для доводки сверл, защищен рамкой. Мотор болгарский, от магнитофона, профиль от витрины, червяк от водопроводного вентиля, подшипники от выдвижного столика.
Свелильный станок 3
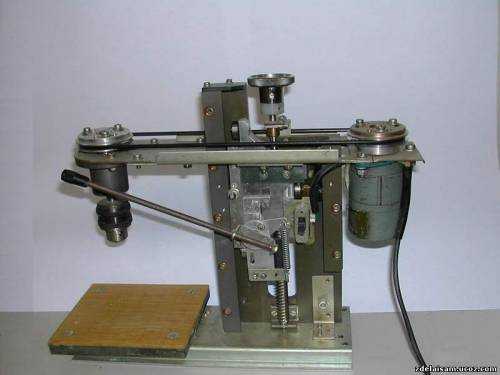
Просто красивый станочек получился. Основа — рамка для линейного перемещения головок 8-дюймового накопителя. На шести подшипниках. Патрон закреплен в втулке от вентилятора этого же накопителя. Червячная передача — от 5-дюймового флоппика, круглая ручка вверху. Последние 20 мм хода сверла — отдельной ручкой. Передача с мотора — резиновый пассик, но лучше плоский ремень. Мотор поставлю посильнее.
Свелильный станок 4
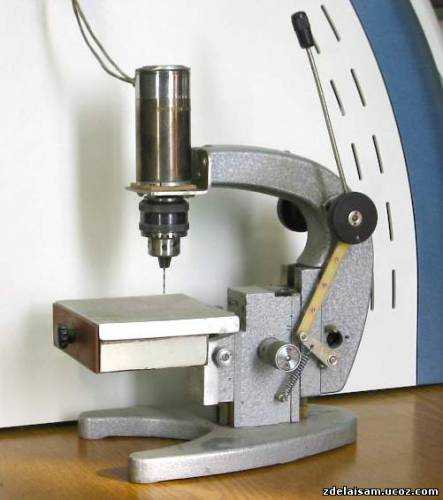
Сверлилка из микроскопа. Один винт перемещает столик под сверла разной длины, второй был поврежден, поэтому на нем сделан ход на последние 20 мм, видны тяги, пружина и ручка. Двигатель ДПР-74. Под столиком ящик для сверл.
Токарный станок
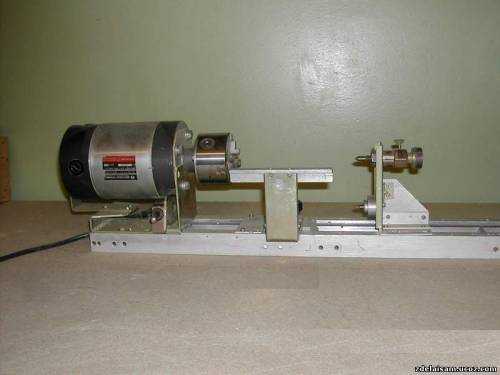
Токарный станок для дерева. Мотор ПИК 12-3/10.1 от болгарского магнитофона/ накопителя. Патрон польский, до 150 мм. Правая бабка с вращающимся центром и подачей на 20 мм. Суппорт фиксируемый, перемещается по горизонтали. Точу на нем ручки для напильников, мелочь вроде солонок, пуговиц. Суппорт получился слабый, вибрирует на твердом дереве, буду переделывать.
Источник: plazon.ru
sdelaysam-svoimirukami.ru
Станина токарного станка по металлу:фото,виды,шабрение и шлифовка
Устройство чугунной станины
фото:устройство чугунной станины
- Продольное ребро;
- Продольное ребро;
- Поперечное ребро, служащее для связи продольных ребер;
- Призматические направляющие продольных ребер;
- Плоские направляющие, которые служат для установки задней и передней бабки, а также для передвижения по ним суппорта;
Стоит отметить, что у направляющих станины поперечное сечение может иметь различные формы. Обязательным правилом является соблюдение параллельного расположения, так что все должно быть равноудаленным от оси центров. Это требует точной фрезеровки или строгания. После этого осуществляется операция по шлифовке и шабрению. Все это обеспечивает точную обработку изделий, а также ликвидацию проблем с передвижением суппорта и возникновением толчков.
Виды станин станков
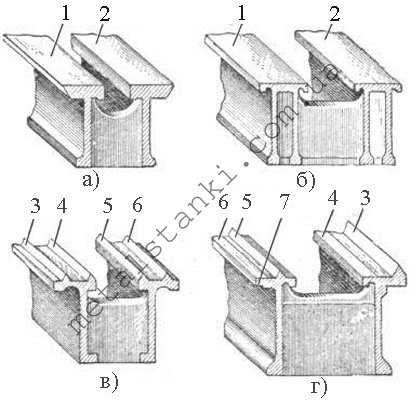
фото:виды станин станков
- Станина токарного станка по металлу, которая представлена на рисунке «а» под номерами 1 и 2, имеет трапецеидальное сечение направляющих. В данном случае основной упор сделан на большую опорную поверхность. Они обладают большой износостойкостью, что позволяет долго оставлять свою точность. В то же время, для перемещения по ним суппорта нужно прилагать множество усилий, особенно, если он перекосился.
- На рисунке «б» представлена станина с плоским прямоугольным сечением направляющих. В отличие от предыдущего, они имеют уже по два ребра жесткости, а не одному, что делает их крепче.
- Рисунок «в» демонстрирует станину с направляющими треугольного сечения. С учетом того, что здесь используется достаточно малая опорная поверхность, с большим весом работать получается сложно, так что данный вид используется преимущественно для малых станков.
- На рисунке «г» показана станина с треугольным сечением и опорной плоскостью. В данном случае она также применяется для станков мелких размеров.
Если станина предназначается для тяжелого станка, то она имеет не только большое сечение, но и большее сопротивление на изгиб. Одними из наиболее распространенных является такой вид, как представлен на рисунке «г». Здесь каретка суппорта делает упор на призму №3 спереди, а сзади упирается на плоскость №6. Чтобы не произошло опрокидывание, ее удерживает плоскость №7. При задаче направления основную роль играет призма №3, тем более, что она воспринимает на себя большую часть давления, осуществляемого резцом.
Если на станине возле передней бабки имеется выемка, то она служит для тог, чтобы обрабатывать изделия большого диаметра. Если же происходит обработка изделия, радиус которых меньше высоты центров, то выемку перекрывают специальным мостиком.
Ремонт станины токарного станка
Шабрение станины токарного станка является технологическим процессом во время которого станина выверяется для закрепления коробки подач при помощи рамного уровня. Благодаря этому можно будет в дальнейшем легко установить перпендикулярность поверхности крепления суппорта и фартука к коробке подач.
- Первым делом станина устанавливается на жесткий фундамент и проверить продольное направление по уровню вдоль поверхности, а поперечное направление по рамному уровню. Допустимые отклонения составляют не более 0,02 мм на 1 метр длины изделия.
- Шабрят верхние поверхности направляющей, сначала с одной стороны, используя поверочную линейку на краску. Во время этого процесса желательно периодически проверять извернутость направляющих.
- Затем шабрят поверхность второй направляющей. Максимальный допуск отклонений здесь остается таким же 0,02 мм на 1 метр длины изделия.
Шлифовка станины токарного станка
Шлифовка станины токарного станка состоит из следующих процедур:
- Необходимо провести зачистку и запиливание задиров и забоин имеющихся на поверхности;
- Станина устанавливается на столе продольно-строгального станка и надежно закрепляются там;
- Далее идет проверка извернутости направляющих, которая производится уложенного на мостике задней бабки уровня;
- Во время установки станины получается небольшой прогиб изделия, который следует исправить путем максимально плотного соприкосновения со столом;
- Повторно проверяется извернутость направляющих, чтобы результаты совпадали с тем, что было до закрепления;
- Только после этого приступают к шлифовке всех контактных поверхностей изделия. Процедура проводится при помощи торца круга чашечной формы. его зернистость должна быть К3 46 или КЧ 46, а твердость соответствовать СМ1К.
www.metalstanki.com.ua
Сколько вы можете заработать на своем фрезерном станке с ЧПУ?
Существует несколько типов покупателей фрезерных станков с ЧПУ. Одни принимают решение о покупке станка в силу необходимости на производстве. В данном случае вопрос можно считать закрытым, станок зарабатывает деньги своему владельцу выпуская продукцию. Другой тип покупателей становится владельцем ЧПУшки вдохновившись многообразием возможностей машины. Ведь на станке можно делать «практически все что угодно». И после того, как розовый туман рассеивается, а первые навыки управления станков получены начинается поиск источников заработка. Способов заработать на станке с ЧПУ масса: изготовление декоративных изделий из дерева, производство мебели, изготовление модельной оснастки. Список можно продолжать долго.
Сегодня я хочу открыть, надеюсь, серию статей посвященных заработку на ЧПУ. В первой статье я расскажу об изготовлении декоративных изделий и продаже их в интернете на специализированных площадках.
На западе очень популярен ресурс для продажи вещей изготовленных своими руками — ETSY. Вот тут мы и попытаем нашу удачу. А для начала изучим образцы работ и их стоимость. А по итогам составим ТОП-10 изделий выполненных на станках с ЧПУ которые можно продать с отличным «наваром». Поехали!
10 место — Монограмма из ореха
Резьба простенькая, но вот отделано не плохо.
Цена: 100 USD
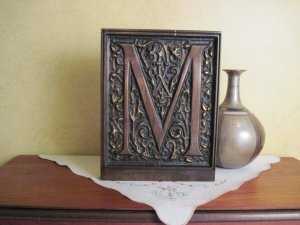
9 место — Настенное панно из сосны
Художественная ценность сомнительна, но тем не менее.
Цена: 260 USD
8 место — Кофейный столик «Темза»
Обычный деревянный щит через который «протекает» вырезанная на фрезерном станке с ЧПУ река Темза.
Цена: 300 USD
7 место — Кому кресло-качалку?
Березовая фанера
Цена: 345 USD
6 место — Привет!
Слово «Привет» из фанеры вырезанное на фрезере с ЧПУ и покрытое «золотым» спреем
Цена: 400 USD
Тот случай, когда слово на вес золота! Хм… Мне всегда казалось, что молчание — золото.
5 место — Журнальный столик в виде сот
В целом ничем не примечательный стол. Его фишка в том, что в центральных сотах есть «мёд» из меди
Цена: 440 USD
Мне кажется, вполне приемлемый ценник за эксклюзивное изделие.
4 место — Декоративная композиция «Винная бочка»
Сей образец сделан из куска старой винной бочки. Рисунок вырезан на станке с ЧПУ
Цена: 550 USD
Скорее всего ценность изделия именно в том, что использовался кусок старой бочки пропитанной вином за долгие годы.
3 место — Настенное панно из клена
Цена: 1400 USD
За что?!
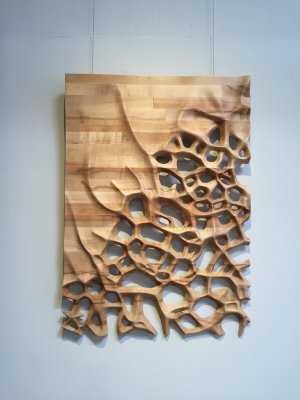
1400 баксов, Карл!
2 место — Стол и стул «Оригами»
Фанера, рояльные петли, стекло.
Цена: 2950 USD
Безусловно, идея крутая, столик легко складывается и раскладывается, но такой ценник мне кажется слегка завышенным. Возможно, я просто ничего не понимаю в искусстве
Да кстати, пару стульев не желаете? Комплект будет. По сходной цене
Цена: 800 USD — За один стул
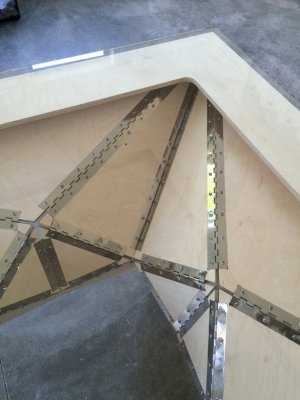
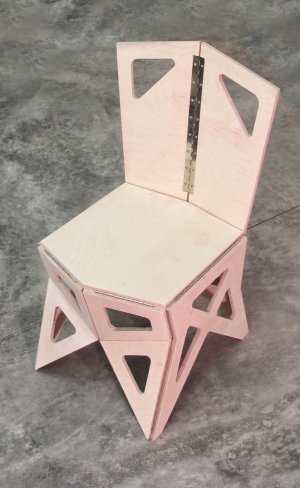
800 Баксов. Это же сколько в рублях по сегодняшнему курсу?!
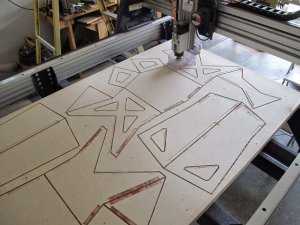
1 место — Картина «День за днем»
Победитель выставил на продажу подложку из МДФ, которую он использовал на своем станке для вырезания деталей. По словам мастера, он использовал ее несколько месяцев в своих проектах. Она ему конечно дорога как память и все такое, но за что такая цена и зачем он ее вообще продает? В общем, как бы там ни было — это хит сегодняшней подборки!
Цена: 5000 USD
И да, я от всей души желаю автору найти покупателя на это произведение техно искусства!
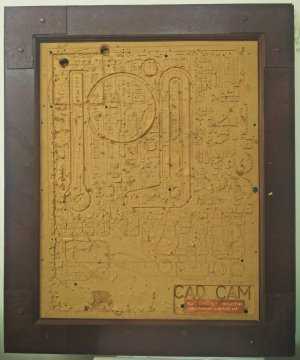
На сегодня это все. Буду еще искать способы заработка на фрезерном станке с ЧПУ и обязательно поделюсь результатами с вами!
www.stankoff.ru
Простой ЧПУ станок часть 1
Перевел alexlevchenko92 для mozgochiny.ru
С тех пор, как я впервые услышал о ЧПУ, мне хотелось сделать такой станок своими руками. В детстве мои родители не приняли всерьез моего увлечения. Они посчитали, что непрактично покупать ЧПУ, поскольку это были всего лишь детские желания. В то время в нашей стране ЧПУ и 3D принтеры не производились, а покупать за рубежом было слишком дорого. По этой причине мне очень хотелось построить свою версию ЧПУ, поэтому я искал в интернете статьи о производстве оборудования такого рода. К счастью, на просторах всемирной паутины были тонны литературы, что касались строительства ЧПУ, но не один из станков не был сделан полностью вручную. Для постройки большинства ЧПУ, необходимо было вырезать много довольно точных деталей, а для этого нужен был ЧПУ станок. Это очень иронично, для производства ЧПУ необходим ЧПУ.
Из-за ограничений во времени при изготовлении станка нужно было импровизировать и использовать общедоступные материалы, что были куплены в строительных магазинах. Все было построено за 3 дня, работы велись и днем, и ночью. При грубом подсчете трудоемкость составила 34 человеко-часов.
Прошу прощения за качество фото. Все снималось на мобильный телефон, поскольку только на завершающем этапе появилось идея выложить статью о том, как сделать ЧПУ станок без ЧПУ станка.
Шаг 1: Мечты, исследования, каракули, макет
Для начала проведем исследования на тему постройки ЧПУ станков. После прочтения десятка статей на тему конструкций, нарисуем эскиз будущего творения.
Шаг 2: Необходимые материалы
Электроника:
- L298N;
- Arduino Uno/ Mega;
- Шаговые двигатели;
- Блок питания.
Материалы:
- Лист ДСП 1,2x2,4 м;
- 4 направляющих длиной по 35 см;
- Пластиковая заготовка для корпуса.
Инструменты:
Шаг 3: Размечаем ДСП
Настало время воплотить рисунки в реальность. Приобретем лист ДСП размерами 1,2x2,4 м и толщиной в 1,3 см. Затем воспользуемся линейкой и маркером для разметки листа.
Шаг 4: Вырежем детали для основной рамы
Лень мешает использовать ручную ножовку? Возьмем электролобзик! ;-). Максимально аккуратно выполним распил листа ДСП. Кривые детали, приведут к снижению производительности станка.
Шаг 5: Результаты
Судя по полученному результату, можно сказать, что проблем в работе основы не будет.
Шаг 6: Очистим рабочее место
Помните! Всегда держите рабочее место в чистоте!
Шаг 7: Установим ползунок оси Y
Механизм работы предельно ясный. Установим ось вместе с кареткой, после чего подключим их к корпусу.
Шаг 8: Усилим раму
К верхней панели добавим кусок древесины перпендикулярный поверхности. Это сделано для увеличения устойчивости, когда станок начинает фрезеровать.
Шаг 9: Поверхности и кромки
Убедимся в том, что поверхность изготовленной рамы достаточно ровная. Это нужно для предотвращения касания движущихся частей о неровную поверхность. Чем меньше трение, тем эффективнее будет работать механизм станка.
Шаг 10: Ножки станка
Возьмём по два квадратных блока ДСП и приклеим их на каждый угол основания. После установки ног, станок поднимется над поверхностью, что создаст возможность монтажа шагового двигателя в основание.
Шаг 11: Монтаж шагового двигателя для оси Y
Отпилим небольшую часть рамы ЧПУ. В этом месте будет установлен шаговый двигатель. Нужно воспользоваться суперклеем для укрепления просверленных отверстий под винтовые соединения.
Шаг 12: Приводящий вал оси Y
В случае необходимости укоротим приводящий вал оси Y с помощью гравера, после чего торец зачистим напильником.
Шаг 13: Соединим вал двигателя с осью
Если вы не нашли муфты нужного диаметра для соединения вала двигателя и оси, можно воспользоваться эпоксидной смолой. Для скрепления частей воедино капнем несколько капель смолы. Держим части вместе до тех пор, пока соединение не затвердеет.
Продолжение следует….
ЧАСТЬ 2
(A-z Source)
ПОДЕЛИТЕСЬ С ДРУЗЬЯМИ!
About alexlevchenko
Ценю в людях честность и открытость. Люблю мастерить разные самоделки. Нравится переводить статьи, ведь кроме того, что узнаешь что-то новое — ещё и даришь другим возможность окунуться в мир самоделок.mozgochiny.ru
Чтобы строить станки — нужны станки!))) С какого начать? — Курилка
Travelller, Хочу иметь возможность изготовить самостоятельно любую деталь не больших размеров и не только для станков. Знаю точно что все станки будут с ЧПУ. Из темы понял, что для начала нужны болгарка и сварочник, с ними я позже разберусь, ну и спасибо всем что ответили что идет первым токарный или фрезерный. Сначала займусь токарным значит. В другой теме спрашивал, но там пока молчат, поэтому спрошу тут. Что лучше делать станок с нуля или оЧПУшить уже готовый станок.
Хочу свой токарный станок с ЧПУ для не большого серийного производства изделий с широким выбором материалов от дерева до титана. Хотел купить не рабочий станок или просто станину с передней бабкой и продольным суппортом, возможно и задняя бабка пригодиться на всякий случай что нибудь длинненькое точить. Затем навесить направляющие поперечные или поперечный суппорт оставить тоже и оЧПУшить все это дело.
Потом посмотрел темы на форумах и различные видео в сети где умельцы собирают токарники с нуля практически. Собственно вопрос как лучше сделать купить готовый и сделать на нем ЧПУ или собирать с нуля. В средствах не особо ограничен, но покупать готовый станок с ЧПУ не хочу, привык все делать на совесть и с запасом прочности. Ну и к тому же творчество))
Нужно будет точить резьбу и передняя бабка под прутки диаметром 50мм. Это уже для конкретных изделий нужно (шары с отверстиями из нержавейки), собственно необходимость их изготовления меня и натолкнуло на мысль о постройке станка.
Не ругайте особо я хоть и разбираюсь в теме уже больше 2-х месяцев, но могу очень многого не знать, хотел посоветоваться с профессионалами. По вопросам:
1. Купить станок и оЧПУшить его или построить с нуля, плюсы, минусы того и другого?
2. На сколько лучше или хуже направляющие хивин и иже с ними их отличие от направляющей самой станины?
3. Если покупать станину под оЧПУшивание, то какую лучше взять? (прочность, вес, размеры, название станка) как я понял ИЖ-и хвалят, чем школьник хуже?
В общем пните в правильном направлении. Я сейчас в самом начале пути, спасибо заранее!))
Детали не большие, мастерская тоже. В общем ничего такого, паровозы и танки делать не собираюсь, если только их модели))
Изменено пользователем denimtorwww.chipmaker.ru
как был изготовлен САМЫЙ ПЕРВЫЙ токарный станок в мире???
Отливали, ковали, потом обрабатывали напильником, камнем
Гончарный круг.
<a href=»/» rel=»nofollow» title=»45989660:##:nozhnoj-privod-tokarnogo-stanka/»>[ссылка заблокирована по решению администрации проекта]</a> сталь на токарном станке смогли обрабатывать только с 1798 года с появлением саппорта <a rel=»nofollow» href=»https://ru.wikipedia.org/wiki/Суппорт» target=»_blank»>https://ru.wikipedia.org/wiki/Суппорт</a> до этого это был лишь чуток модернизированный гончарный круг. крепкие валы и шестерёнки токарному станку не критичны, не ими же режут. их вообще из дерева делать можно. режут лишь режущей частью. срач по твоему вопросу: <a href=»/» rel=»nofollow» title=»45989660:##:gravyura/#comment-68316″>[ссылка заблокирована по решению администрации проекта]</a> «Токарный станок известен с древнейших времен — тот же гончарный круг, является таковым. Но были в истории два изобретателя, имена которых упоминаются редко, звали их Джозеф Брама и его ученик Генри Модслей — они модернизировали токарный станок, изобрели «скользящий упор», в простонародье суппорт. Произошло это в 1794 г. от Рождества Христова=)) Именно эту дату и стоит считать началом промышленной революции. Именно изобретение суппорта и дало возможность промышленного производства высокоточных деталей, для паровых машин в частности. Более того, Модслей из токарного станка сделал токарно-винторезный, механически связав движение каретки с вращением шпинделя. До него винты резались вручную это было долгое, нудное и очень трудоемкое развлечение — он и сам был искусстным мастером по этому делу. Видать достало оно его, он сделал самый точный винт который мог, вставил его в станок, и нарезал винт с такими же параметрами в станке. «Новый винт оказался намного точнее, и Модслей с радостью забраковал свою собственную ручную работу, выбросил из станка старый винт, поставил новый, изготовленный на станке, и… снова нарезал еще один, третий винт. Конечно, настойчивый изобретатель на этот раз получил еще лучшие результаты: ведь резец правильнее, точнее перемещался вдоль изделия. Еще и еще раз Модслей менял ходовые винты в своем станке, пока, наконец, не получил подряд два одинаковых по точности изготовления ходовых винта. » Этот день в истории можно считать днем рождения взаимозаменяемости. «
А этот чел что получается, так мимо проходил? (great-country.ru/content/sov_nauka/mi_first/mi_0028.php)
Ручной станок с педалью как у швейной машинки
touch.otvet.mail.ru
конструкция, предназначение и варианты изготовления своими руками
Ни один домашний мастер-умелец не обходится без ручных электроинструментов. Но иногда наступает момент, когда такого инструмента бывает мало, и требуется помощь серьезного оборудования. Так, например, обработать поверхности больших деталей способен ленточный шлифовальный станок. Промышленные агрегаты стоят слишком дорого, поэтому многие мастера делают шлифовальные станки своими руками.Конструкция ленточного шлифовального станка
Дерево широко используется для изготовления всевозможных изделий и деталей. Для того чтобы обработать деревянную заготовку должным образом, используется различное оборудование. Тщательную высокоточную обработку дерева производят на ленточных шлифовальных станках, которые в качестве рабочего органа имеют абразивную ленту.
В конструкции шлифовального агрегата предусмотрены:
- Абразивная лента, которая может располагаться горизонтально или вертикально. Она устанавливается на станине и размещается между вращающимися барабанами.
- Ведущий и ведомый барабаны. Вращение ведущего барабана происходит за счет электрического двигателя, который передает вращательный момент через ременную передачу. Скорость вращения ведущего элемента, а значит и скорость движения ленты можно регулировать специально установленными режимами обработки поверхностей.
- Стол оборудования может быть деревянным или металлическим. На выполненном из металла основании можно затачивать более сложные заготовки.
- Электрический двигатель должен иметь мощность около 2,8 кВт и быть способен обеспечить ленте нормальную скорость в 20 метров в секунду.
- Специальная монтажная вытяжка должна быть установлена для того, чтобы во время технологического процесса можно было удалять образующуюся во время работы пыль.
Длина станка и его рабочего инструмента зависит от длины изделий, которые будут на нем обрабатываться. Намного удобней работать с заготовками, которые имеют меньшую длину, чем рабочая поверхность.
Для чего нужны шлифовальные станки?
Как правило, оборудование применяется для чистовой механической обработки изделий на заключительных этапах производства. Работать ленточные шлифовальные станки могут как с деревом, так и с металлом.Оборудование по дереву способно окончательно выравнивать поверхности, удалять шероховатости и неровности в виде возвышений или углублений, обдирать заусенцы, шлифовать закругления, делать внутреннюю шлифовку, добиваться ровных и гладких поверхностей изделия.
Станки по металлу работают с цветными металлами в виде плоских, круглых и четырехугольных заготовок и с простой и легированной сталью. Они способны рационально и за короткое время отшлифовать большого диаметра трубы и кругляки.
Кроме этого, ленточные шлифовальные станки предназначаются:
- для шлифования изделий перед процедурой лакокрасочного покрытия;
- для обработки брусковых и щитовых заготовок, их боковых кромок и торцов;
- для обработки плоских поверхностей;
- для шлифования криволинейных поверхностей.
Инструкция по изготовлению
Изучив конструкцию оборудования, следует определиться, из чего будут выполнены его основные элементы.
Из чего сделать станину?
Лучше всего рабочий стол выполнить из толстого железа. Идеальные габариты полотна – 500х180х20 мм. Однако чем больше габариты станины, тем больше вариантов различных деталей на ней можно будет обработать.Большая рабочая поверхность будет намного удобней и функциональней маленькой станины. Для ее изготовления понадобится:
- Одну из сторон подготовленного для стола полотна обрезать с помощью фрезерного станка по металлу.
- Сделать разметку.
- В торце обрезанной заготовки просверлить три отверстия.
- С помощью трех болтов закрепить рабочую площадку на станине.
Выбор и установка двигателя для станка
Двигателем для агрегата может служить мотор от стиральной машинки. Если такого в наличии нет, то можно подобрать мотор, номинальная мощность которого будет составлять до 3 кВт, а интенсивность работы – около 1500 об/мин. Силовой агрегат для шлифовального станка следует плотно и надежно зафиксировать на станине.
Ведущий и ведомый барабаны
Такие элементы для шлифовального станка изготовить своими руками можно из такого материала, как ДСП. Для этого необходимо:
- Выпилить из листа ДСП заготовки размерами 200х200 мм.
- Собрать из полученных заготовок пакет толщиной в 240 мм.
- Все сложить и проточить до оптимального диаметра в 200 мм.
- Закрепить ведущий барабан на валу двигателя. Он будет приводить в движение ленту.
- Ведомый барабан закрепить вокруг станичной оси на подшипниках. При этом со стороны барабана должен быть специальный скос. Это поможет обеспечить ленте мягкое касание к рабочей поверхности.
Изготавливая барабаны, стоит учесть, что диаметр их центральной части должен быть на пару миллиметров больше наружного диаметра. Необходимо это для обеспечения стабильной работы техники, так как гибкая лента будет находиться в середине барабана.
Шлифовальная лента своими руками
В качестве шлифовальной ленты можно взять несколько наждачных полос. Их нужно будет разрезать на кусочки длиной в 200 мм и склеить. Идеальным вариантом основы для полотна будет брезент.Проклеивать изделие своими руками рекомендуется качественным продуктом, который будет способен сохранить целостность элемента длительное время.
Некоторые мастера рекомендуют обтягивать катки резиной. Для этого можно использовать камеры от мопедов или велосипедов. Толщина резинового слоя должна быть около 30 мм.
Собрав из всех подобранных элементов конструкцию, можно смело приступать к обработке древесины.
Шлифовальный станок из ручной шлифовальной машинки
Взяв за основу ручную шлифовальную машинку, остальные детали оборудования можно своими руками выполнить из ДСП, сосновых и березовых брусков. П-образный упор склеивается клеем ПВА, остальные элементы агрегата соединяются шурупами.
Основанием станка могут послужить соединенные петлями два куска ДСП. Для большей прочности петли крепятся болтами М6.
Шлифовальная машинка к основанию устанавливается с помощью брусков, которые заранее подгоняются по форме корпуса и сверху проклеиваются кусочками резины.
Спереди шлифмашинка крепится подходящего размера мебельными конфирмантами. С их помощью шлифовальную плоскость можно будет выставить в нужном положении.
Сзади к основанию машинка крепится бруском и двумя шурупами. Чтобы упорная площадка со шлифовальной плоскостью находилась на одной линии, под корпус можно приклеить кусочки мягкой резины.
В горизонтальной части П-образного упора можно сделать паз для перемещения маленькой каретки, которая может пригодиться для заточки ножей электрорубанка.
После закрепления и регулировки шлифмашинки станок можно начинать эксплуатировать.
Изучив варианты изготовления ленточного шлифовального станка своими руками, и четко следуя инструкции, можно обзавестись многофункциональной техникой. Такое оборудование способно будет не только шлифовать изделия из дерева, но и затачивать любые режущие инструменты.
Оцените статью: Поделитесь с друзьями!stanok.guru